Powertrain Control
The engine industry finds itself in a position where the end of ever-increasing system complexity is far beyond the horizon. The advent of novel combustion technologies, hybrid powertrains, and re-thought engine paradigms poses the challenge of keeping it all together. This is exactly what the Control subgroup aims to do.
The Control subgroup strives to find efficient solutions for the contemporary challenges in the industry. We seek to effectively bring together the latest advancements in the EPS research group and employ the cutting-edge knowledge in Control theory to open new horizons in powertrain control. We strive to establish a bridge between academic research outcomes and industrial expertise through close collaboration with industrial partners. We acknowledge the industry’s dire need for methods to reduce the carbon and noise footprints of modern powertrains and offer creative solutions for their use.
Our current research engages in control methods for novel engine mechanics and combustion control. We are experts in utilising model-based and rapid prototyping control designs to pair our technical knowledge with practical implementation. Through implementing the solutions as proof-of-concept demonstrations and absorbing new findings in the fundamental front of energy systems, the Control subgroup creates a positive loop of evolution.
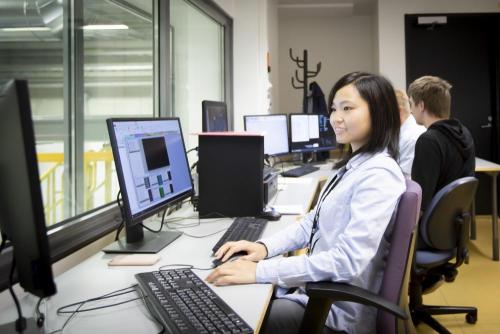
Research interests and methodologies
Our research interests can be divided into five categories:
• Optimising engine control, including fuel consumption, emissions, and aligning with noise legislation
• Creating advanced combustion concept control design
• Delivering adequate aftertreatment control design
• Facilitating fuel-flexible control system development
• Integrating adaptively for the hybrid-energy production solution
Our high ambitions in the field of powertrain control are supported by both state-of-the-art infrastructure and greatly valued collaboration with other universities and industrial partners. These resources allow us to access cutting-edge methodologies:
• Model-based control design
• Rapid prototyping control design
• Model in the loop (MiL) and hardware in the loop (HiL) simulation
• Experimental testing with different engine research platforms